
Welcome to our primer on our award winning saw blades.
We'll talk about how we design and manufacture our Infinity Tools saw blades. Learn about the entire manufacturing process; from steel and carbide selection to quality control and also get a first hand look at pictures of our saw blades being produced in a state-of-the-art European facility.
We'll also go into the design of the blade talking about tooth count, tooth configuration and rake angles, gullets, and extra features like anti-vibration and expansion slots. Our third post will teach you how to choose the best blade for your application, the features you should look for in a quality saw blade and discuss different types of blades available.
Lastly, we'll give you some clever hints and practical advice on choosing the style of blade that will work best for your job, as well as a great chart to help in saw blade selection. This is useful information for all woodworkers and the chart makes quick work of choosing which blade is right for your machine and application.
If you're a woodworker that wants the best saw blade for every job or you're curious as to what goes into making the best saw blades, you should spend a minute and read this post. Thanks for your interest and please leave us a comment to tell us what you think!
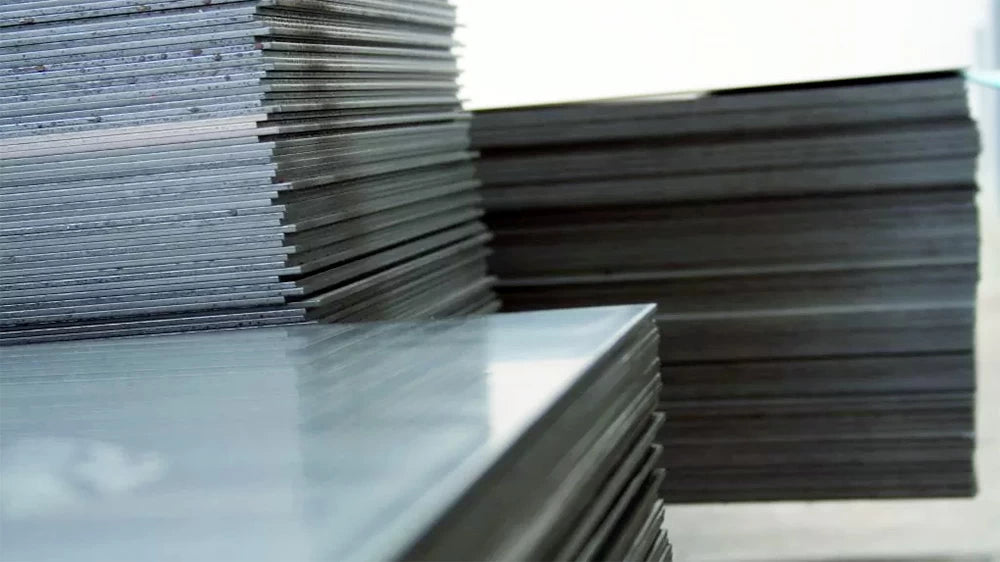
Premium quality saw blades begin with the finest raw materials
Infinity Tools saw blades are designed to offer superb cuts, reliable performance and extended cutting life. We achieve this by manufacturing saw blades that only use the highest quality materials, manufacturing techniques and employ advanced design.
Cold-Rolled Steel
We only use Cold-Rolled steel for the production of our circular saw blades. Inferior quality saw blade manufacturers will use hot-rolled steel since it is cheaper and faster to machine. But the process of hot-rolling creates a steel plate which does not perform under the stresses of woodworking. Conversely, cold-rolled steel is pressed at a temperature where the plasticity of the steel is still high. This allows the material to maintain ductility, providing resistance to deformation and forming the ideal foundation for our premium quality saw blades.

Premium Micro-Grain Carbide Tips
A circular saw blade is only as good as its cutting edges. That’s why we only use micrograin carbide tips from Ceratizit, the leader in sintered carbide technologies. Their exclusive SinterHIP sintering process make it possible to obtain a premium virgin grade of carbide that is practically free of porosity. A carbide tooth which is non-porous will resist cracking much better than once produced with a lower cost process. We use this premium carbide on all of our woodworking saw blades so you can be sure they will go the distance in your shop or on the job site.
State-Of-The-Art Manufacturing & Advanced Saw Blade Design:
Precision laser cut saw blade plate - We use a very precise CNC laser-cutting machine to accurately form each blade body. This advanced manufacturing technique allows us to produce a saw blade body that is 5x more accurate than one that comes out of a high-volume press or mold. Laser cutting is the ideal method for making blade bodies since it’s possible to cut the plate within tighter tolerances and to use higher-quality steel plates during the production process.
Thermal heat treatment - A blade plate that contains stresses and molecular non-uniformity will distort and warp when cutting wood. To avoid these potential problems, each of our saw blade plates undergoes a complex annealing process in a closely controlled computerized oven. This extra step in our quality process relieves internal stresses while making the saw blade resistant to warping when working. The end result is a saw blade that runs true and free of distortion when cutting wood.
Flattening of the plate and hand flatness testing - A critically important step in making a premium quality blade is to ensure it's flatness. A blade that is not flat will not cut well. We have a special machine that ensures each saw blade plate is flat to within .002”. Once flattened, each plate is then checked by hand to ensure its parallelism and planarity to within (± 0,01mm). Each saw blade plate must fall within these very tight tolerances or the body is reworked and checked again.
Tension of the plate and hand tension testing - Blade bodies spinning at 8000 r.pm have a tendency to warp or distort under this immense pressure. Tensioning a blade body allows it to stay true while spinning on your saw and minimizes runout. It is an essential part of our quality production process and done properly, it ensures maximum performance in each of our saw blades.
Carbide teeth are affixed to steel bodies through a process called "Brazing" - We use a special Tri-Metal brazing material which forms an unbreakable bond between the steel plate and the micro-grain carbide tooth. The Silver component of this braze material melts at a lower temperature and thus allows us to introduce less stress during the brazing process. Our fully automatic brazing stations are aided by lasers to obtain perfect tip placement on the steel body and the strongest joint possible. Another important feature of tri-metallic alloy is that it acts as a shock buffer and substantially reduces the effect of the micro-impacts that the cutting edges take during operation. This leads to longer tooth life and increased time between sharpening.
Nickel-Armor or Teflon coating - Nickel Coatings have long been prized for their strength and durability in high tech industries. In fact, the Aerospace industry coats aircraft parts, including engine components and landing gear pieces with Nickel because of its excellent lubricity, wear resistance and anti-corrosive properties. These properties are exactly what you want in a top-quality saw blade which is why we are proud to exclusively offer Nickel-Armor coatings on all of our woodworking saw blades.
Carbide Grinding - Carbide grinding is arguably the most important part of producing a top-quality saw blade. Experience has shown us that the sharper a tool is, the longer it will last and the cleaner it will cut. This is why we employ an array of 5-Axis C.N.C. carbide grinders equipped with high-pressure oil cooling and extra-fine diamond grinding wheels . These special machines allow us to apply a final mirror-finish grind on each carbide tooth that ensures the sharpest and longest lasting cutting edge possible.
Do you know what the "Golden Rule" is? If not, keep reading and you'll discover the differences in tooth count, tooth configurations, and why gullets and expansion slots are important to blade performance. Good quality circular saw blade design is as important as using the best raw materials and production techniques and making sure you've got the right saw blade for the job will make a big difference. Read below to learn more about choosing the best saw blades for your shop.
Some Talk About Teeth
The number of teeth on a saw blade and their shape is one of the more significant aspects of its design. Tooth count should be based on an intended application and the other parameters of the blade. If all other parameters are equal, more teeth will equate to a cleaner cut but there are several other factors that influence cutting performance. For every design choice there are pros and cons, and more teeth is not always better. More teeth also means more friction and heat, more resistance to the saw, slower feed rates, and a higher chance of burning on some materials. Inversely, fewer teeth tend to mean faster more efficient cutting, but usually also means a rougher cut.

The Golden Rule Of Blade Selection
It's important to match the thickness of your stock to a blade that has the correct amount of teeth, we call this "The Golden Rule". For wood cutting applications, depending on the thickness of the material, it’s recommended to have 5 to 7 teeth of the saw blade in the material for crosscutting and finish cuts. For ripping applications, 3 to 5 teeth of the saw blade are recommended. So if you're ripping a 1/2" thick piece of stock make sure the blade you're using has at least 3-5 teeth engaged in the cut at any time. If your 24 tooth ripping saw blade won't allow for this, change to a blade with more teeth for a smoother rip cut. On a typical 10” diameter saw blade, it’s common to see 10 to 30 teeth on dedicated ripping blades.
Specialized cross cut blades for plywood, laminates, veneers and melamine commonly have 60 to 100 teeth. Saw blades with higher tooth count cost more to produce, more to buy, and more to sharpen but more teeth also share the workload that helps extend the edge life between sharpenings.
Tooth Configuration
Flat Top - Flat top teeth are used on blades intended primarily for ripping wood with the grain. A flat top grind (FTG) is very efficient at removing large chips from the kerf, and is a very durable grind that tends to have very good edge life. A flat top grind is the only grind that will leave a truly flat bottom kerf, which also makes it a good choice for cutting grooves and splines. The FTG is commonly found on ripping blades with a steep positive hook angle and lower tooth count, typically 10 to 30 teeth. Click here to see Infinity Tools Ripping Saw Blades.
ATB - Alternate Top Bevel (ATB) is a very versatile grind that features a bevel across the top of the tooth that angles from the outside in, alternating between left side and right side. The angle of the bevel can vary from about 10° to upwards of 25°. The versatility of the ATB grind makes it a very common grind on many types of blades, especially woodworking blades. The bevel helps reduce tear-out on cross-grain and plywood cuts, is reasonably durable, and can still be fairly efficient at ripping with the grain. Essentially the steeper the bevel angle, the less tear out the teeth will cause, but also becoming increasing less efficient at ripping as the bevel increases. The ATB grind is very well suited in a configuration as a higher tooth count dedicated crosscut blade, and as a versatile medium tooth count general purpose blade. Click here to see Infinity Tools ATB Saw Blades.
Hi-ATB – A variation of the ATB grind, teeth with a top bevel of roughly 25° or higher are commonly referred to as High Alternate Top Bevel grinds. Hi-ATB grinds have the lowest tear-out characteristics of any other grind, and are extremely well suited for clean cuts in plywood, laminates, melamine, veneers, and ultra-fine crosscuts in hardwood. The sharp points of the higher bevels give up some durability and some ripping efficiency compared to some grinds, but are still capable of good ripping efficiency when combined with a lower tooth count and positive hook angle. Click here to see Infinity Tools Ultra-Smooth Crosscutting Blades.

ATB/R Combination – The ATB/R grind is a combination of two different tooth grinds in one blade. It typically features groupings of five teeth that consist of four ATB ground teeth and one flat top “raker” tooth with large gullets between the groupings. Common configurations are found in a 10” blade with 50 teeth and a moderately steep hook angle of 10° to 15°. Most ATB/R designs feature the raker tooth at the front of the 5-tooth grouping, but Infinity’s Combomax design moves the raker in between the four ATB teeth to help reduce saw marks that are commonly caused by the raker tooth. Infinity also puts slightly chamfered corners at the top of the raker tooth to further reduce saw marks and reduce tear out characteristics. This configuration is designed to offer a versatile combination of good ripping and good crosscut characteristics. It’s well suited for general-purpose woodworking applications on a table saw or compound miter saw. Click here to see Infinity Tools Combination Saw Blades.
TCG–The triple chip grind (TCG) also combines two different tooth grinds in one blade – a flat top grind and a trapezoidal grind, which is essentially a flat top tooth with chamfered top. The TCG alternates between a flat top “raker” and the trapezoidal tooth that protrudes slightly above the raker tooth. The TCG is extremely durable, and exhibits low chip out characteristics in brittle materials, which makes it well suited for cutting metals, laminate flooring, very hard woods, abrasive materials like MDF and teak, and sheet goods like melamine. Its durability also lends itself to high volume applications where edge life is important. Click here to see Infinity Tools Multi-Material Saw Blades.

Other Critical Design Elements
Gullet - A gullet is the space between the teeth on a saw blade. One of the reasons a saw blade with fewer teeth will cut faster is that there is more gullet space in front of each tooth, which allows for better chip removal. Ripping operations have larger chip size than crosscutting operations, which makes lower tooth count blades with their lower resistance and larger gullet space more conducive to that type of operation. Crosscutting operations tend to make smaller chip sizes, so a specialized crosscut blade can have more teeth around the perimeter of the blade, allowing for a cleaner cut.
Anti-vibration & Expansion slots - Laser cut expansion slots help channel heat build-up during the cutting process, allowing the blade to expand and contract without distorting and destroying the tension of blade’s body. Anti-vibration slots absorb noise and help the blade run quiet and true by not allowing harmonic distortion to reach the cutting teeth. Filling the slots with silicone can further reduce noise.

Hook Angle - Hook angle (or rake) is the amount of forward or backward lean of the teeth on a blade. Saw blade hook angle can range from -7° to as much as + 22°. The steeper the hook angle, the more aggressive and faster the feed rate will be. A positive hook angle (forward) will have more pull on the material than a low or negative hook blade, which is a feature best suited for ripping operations on a table saw. A low to negative hook blade is well suited for a sliding compound miter saw (SCMS) or radial arm saw (RAS) to prevent “climb” or self feeding of the material, and is especially important when cutting metals on any type of saw. Saw blades with positive hook angles will feed faster but can also increase tear out characteristics at the exit of the cut. Saw blades with a lower hook angle will have lower tear-out tendencies but will require increased feed pressure. This style of blade may have a higher tendency to burn, exposing inaccurate machine setup or technique.

Saw Blade Selection
Saw blade selection is very much proprietary to your saw, what you cut, and your cutting objectives. The basic signs of top quality are characteristics like premium materials, precision construction and advanced design. Good fit and finish, large polished carbide tips, C.N.C. laser cut heavy steel plate, and coatings are not a guarantee of high quality but they are a strong indicator that a premium blade was the intent of the manufacturer. Some saw blades are better suited for certain applications and work best on specific types of saws. Blades for the table saw tend to have a positive hook angle while blades for a sliding compound miter saw (SCMS) and radial arm saw (RAS) tend to have a very low to negative hook angle. There are different blade designs for wood, plywood, melamine, laminates, MDF, plastics, and non-ferrous metals. Look for a blade that’s recommended for the type of saw you own and the applications that you intend to use it for. Choosing appropriate saw blades and cutters is among the most important choices you will make for the performance and safety of any tool. Infinity saw blades are designed to offer superb cuts, reliable performance and extended cutting life. We achieve this by manufacturing saw blades that only use the highest quality materials, manufacturing techniques and employ advanced design.
Saw Blade Recommendations
Table Saw Blades - Table saws are used to perform both ripping and crosscutting operations. One important decision for saw owners to make is whether to choose separate task-specific blades that have excellent performance in a specific application but have limited versatility or use a general-purpose blade that will give good results in most applications. There’s merit to both philosophies depending on the situation, your preference, budget, and cutting objectives. Note that a saw blade with better performance in one aspect of cutting doesn’t necessarily mean it’s a better choice for your needs overall.
Many types of cuts, many types of blades - Using task-specific blades requires owning at least two saw blades (typically a 24T rip blade and a 60T or 80T crosscut blade) that each excel in a limited operating region, and are not ideal for tasks outside of their intended scope. It also requires blade changes for each different task to achieve optimum results. Two task-specific blades will generally stay sharp longer than a single general purpose blade because the workload is shared by more teeth. A general-purpose saw blade will neither rip as efficiently in thick material as a dedicated rip blade, nor cut as cleanly as a dedicated crosscut blade, but you may find that it’s more than acceptable at doing both tasks for most situations. However, a high-quality general purpose blade will leave a cleaner edge than the rip blade, will crosscut faster than a crosscut saw blade and will do so with the convenience and cost savings of using only one blade. A high-quality general-purpose saw blade will leave a glue-ready edge. If you happen to do a lot of specialty cutting of fine veneered plywoods, veneers, melamine, MDF, plastics, etc., or need very fine cuts, a specialty task-specific saw blade is recommended. If you tend to rip very thick dense materials regularly, then a dedicated ripping blade is a wise choice. Ultimately for table saw use, having a dedicated rip blade, a dedicated crosscut/plywood blade, and a high-quality general purpose blade will cover the vast majority of cutting needs. We have several saw blade package deals that include specialized saw blades in one money-saving package.

Ripping Blades - Ripping operations are cuts that go with the wood grain. They can require a lot of power from your saw, and an appropriate ripping saw blade can make a significant difference to both the saw and the quality of the cut. For efficiency, ripping blades typically have lower tooth counts than any other type of saw blade (which inherently gives them larger gullets), frequently feature FTG teeth, and have a steep positive hook angle to ease the required feed pressure of pushing a board through the blade. If your saw is less than 3hp, a good thin kerf rip blade can be advantageous. Suggestions: Infinity 010-024 or Infinity 010-124 for saws under 3hp.

Crosscutting Blades - Crosscutting operations are cuts that go across the wood grain. Cuts across the grain are inherently more prone to tear out than cuts with the grain, so a blade with more teeth that sheers the fibers is best. Blades with 60 to 80 teeth with an ATB or Hi-ATB grind, and a moderate hook angle are best suited for crosscuts. The same characteristics are also desirable for ultra-fine plywood cuts. Suggestions: Infinity 010-180 or Infinity 010-080.

General Purpose Saw Blades - General Purpose Blades are designed to perform all table saw operations with satisfactory results. Typical general purpose blade configurations include 40T ATB blades with steep hook angles, and 50T ATB/R combination blades. Both will give smooth efficient rip cuts, and low tear out crosscuts in most situations, and are similarly versatile in plywood and sheet goods. Suggestions: Infinity 010-044 Super General, Infinity 010-050 Combomax or Infinity 010-150 Combomax Lite for saws under 3hp.

Radial Arm Saw (RAS) and Sliding Compound Saw (SCMS) Blades - The sliding action of a RAS and SCMS require a blade with a hook angle range of negative, to low positive (approximately -7° to +7°) to prevent “climb” or self feeding of the work piece. Most blades with a suitable hook angle have a medium to high tooth count, often in the 60T to 80T range. You can choose from a Hi-ATB grind for the lowest possible tearout, 010-280, or a Triple Chip grind (TCG) 010-380 for best durability. A blade with a flat top raker combined with either a Hi-ATB or ATB grind to increase durability while retaining low tearout characteristics is also a good choice, 010-280. The latter configuration is especially well suited to handle the chopping action of a compound miter saw (CMS). Suggestions: 012-190, or 010-080.
Thin-kerf vs. Full kerf blades - The kerf of the saw blade is essentially the width of the widest part of the face of carbide teeth, and equates directly to the cutting width of the blade. Saw blades fall into two kerf classifications – full kerf or thin kerf (TK), but there are exceptions. Most full kerf saw blades have wider teeth and proportionately wider body plates than thin kerf blades and are commonly in the range of 1/8” wide (~0.125”, ranging from roughly 0.111” to 0.145”), while most thin kerf blades are about 3/32” wide (0.094”, ranging from roughly 0.090” to 0.106”). Full kerf saw blades tend to be more stable than their TK counterparts due to the increased steel thickness and body mass but require more power to spin. The wider the kerf, the more power required to pass the blade through the material. There will also be a proportionately higher amount of sawdust from a full kerf blade, more wood consumed in the process, and somewhat higher noise levels. The heavier mass of a full kerf plate will handle the stresses of heat better than a TK blade, so is often a more suitable choice for high volume applications. If you’re using a saw that’s under 3hp, a TK blade will pose less resistance to your saw. A high-quality thin kerf blade with proper tensioning of the body during manufacturing will rival the cut quality and performance of a high-quality full kerf blade, and can be a very suitable choice for a home shop, smaller saws, and even in many commercial settings where wood consumption is a concern. Which width to choose depends a lot on your saw and the material being cut.
Why should you buy a top-quality saw blade?
If your saw is well made and properly designed to spin true, the end performance will be largely determined by setup and blade selection. The saw will only be as good as the saw blade that’s put on it, so choose wisely. A high quality saw blade will perform better, stay sharp longer, and is worth having sharpened many times. As always, high quality tools are a wise investment.
Use the table below to find the right saw blade for your next job. If you still have questions regarding saw blade selection, please click here to email us and we'll respond promptly. Thanks for your interest in our woodworking saw blades.

* Legend
FTG = Flat Top Grind
ATB = Alternate Top Bevel
ATB+R = Alternate Top Bevel Plus Chamfered Raker Tooth
ATB w/SSG = Alternate Top Bevel with Super Side Grind
HiATB = High Alternate Top Bevel
TCG = Triple Chip Grind
Continue To Part 2