
Cabinetry is without a doubt the most popular form of woodworking. The term cabinetry refers to the style of woodwork for everything from kitchen cabinets, bathroom vanities, and any form of built-in cabinet work found in residential and commercial applications. While relatively simple, cabinetry does require precision and attention to detail. With a few tips and tricks almost any woodworker can complete major projects with basic tools in your woodworking shop.
We decided to remodel our shop here at Infinity Cutting Tools and replace the hodge-podge of shelves and cabinets with a new wall of custom-built cabinets. This gave us the opportunity not only to organize our shop but document the process to help others looking to tackle similar projects.

The first step is to plan your project and create a materials list. This is where all the decision-making happens. Cabinet sizes, type of wood, finish, hardware -- all of this should be figured out before the first board is cut or even ordered. Sizing cabinet boxes depends on how and where you're installing the cabinets. We made six wall cabinets and six base cabinets all measuring 36"-wide using traditional face frame construction. We used high-quality, 3/4"-thick Baltic birch plywood that comes in 5' x 5' sheets rather than the more traditional 4' x 8' sheets. The size difference affects your part layout on the cutting diagrams so be sure to take this into account when designing your cabinets. If necessary, you can slightly alter the dimensions to make better use of the material for less waste.

To figure your materials you will need to draw up a floor plan for the project and elevation, especially for kitchen cabinets. You may also need to know the dimensions of appliances and height restrictions such as minimum clearances over the stove. With this information, you can draw out the sizes of each cabinet box. Our project was straightforward because all the boxes were the same 36" width. I took the time to draw out my cut sheet so that each piece needed for the project was accounted for.
The cut sheet serves two purposes. First, it ensures that enough material is purchased. It also acts as a roadmap when the cutting begins to make sure the best yield is achieved. I also label each piece as it's cut so I know where it goes when it's time to assemble the cabinets.

With all the materials considered, we also need to consider what tools will be needed to build the basic plywood boxes. This depends on how much of the work you plan to do yourself. Must-have tools include:
- Table saw with a rip capacity to handle the widest piece
- Zero-clearance inserts for your table saw
- Portable drill
- Kreg pocket hole jig
- Clamps for assembly
I also strongly recommend investing in a few good quality saw blades including a rip, crosscut, and general-purpose blade. You'll also want to make sure your table saw is outfitted with a zero-clearance insert. This eliminates tear out, especially when cutting plywood.
Later on, you'll need a router table and a set of rail-and-stile router bits and a raised panel router bit to make the doors and drawer fronts. We'll talk more about that in a later post.

Base Cabinet Box Construction
The base cabinet box consists of eight pieces, not including the face frame. The total depth of the plywood box without the face frame will be 23-1/4". The box is made from two sides, a bottom, four plywood strips roughly 4" wide that support the back and top, and the 1/4" plywood back. All pieces are assembled using pocket screws. The back is slid into a groove cut into the bottom, sides, and one of the top strips with an Infinty 1/4"-Kerf Flat-Top Table Saw Blade to capture the 1/4" plywood back.

All the pocket screw holes are drilled on the outside of the cabinet box for a couple of reasons. Drilling from the outside face angles the screw away from the edge of the plywood giving the screw more holding power. It also gives the inside of the cabinet box a clean appearance. I recommend marking the location of each pocket hole that needs to be drilled on each piece of the box. That speeds up the drilling process and ensures that you don't forget to add a pocket, or accidentally put one in the wrong place.

I also recommend investing in a pair of Kreg right-angle clamps. These clamps have a round peg on one side that fits into a pocket hole and clamps the two pieces together. Clamping is extremely important when using pocket screws. Because the screws go in at a slight angle the pieces may shift and not be aligned properly.
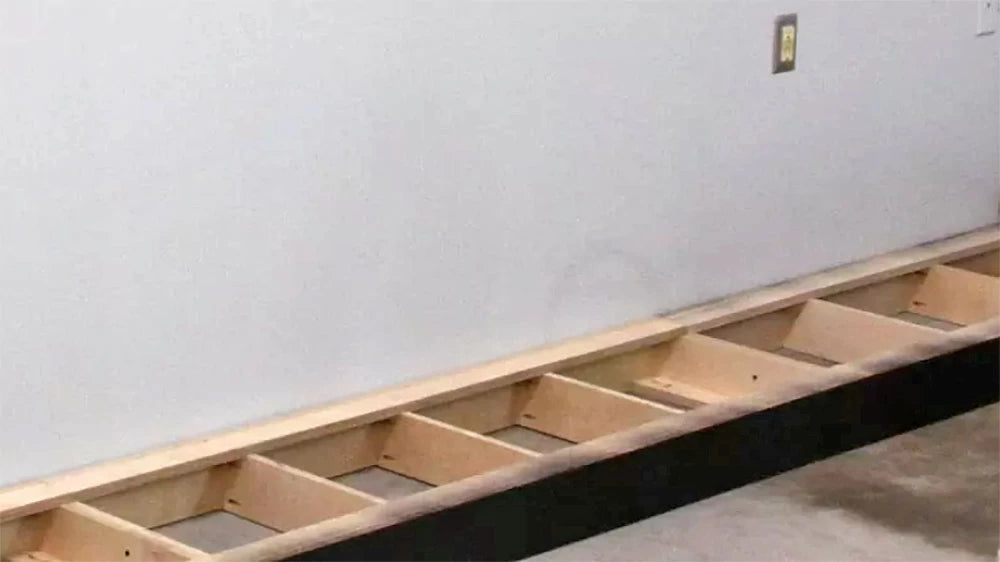
Toe Kick
When building lower cabinet boxes I prefer to use a two-piece construction method. This means that the toe kick and the cabinet itself are two different pieces. This method has some distinct advantages over a one-piece construction. First, it allows for a solid base that is easy to attach to the floor and/or wall that is easy to make level. The toe kick can be made in long sections, making it quick and easy to assemble and install. It also means that there are no notches or inside corners that have to be created in the cabinet box sides, making the cabinet box easier to construct.
All a toe kick needs to be is a box of the correct height, with a flange on the bottom that can be shimmed to level and attached to the floor. I also installed two flanges on the top side that are used to attach the cabinet box with screws. Beyond these two requirements, it only needs to be the correct width and length to create the setback or overhang for the desired look. for ours, we chose a relatively standard 4"-tall x 20"-deep toe kick assembly which provides a 4" cabinet overhang. Using the Kreg K5 pocket hole jig and Kreg right-angle clamps to assemble the toe-kick box makes construction strong and simple.
Wall Cabinet Box Construction
The upper wall cabinet boxes are assembled in the same way as the base cabinets. A wall cabinet box consists of seen pieces, not including the face frame: Two sides, top, bottom, two back strips, and the 1/4" plywood back. The only differences between the base and wall cabinet box are that the wall cabinet is shallower (11-1/4"-deep) and has a solid plywood top. Like the base cabinets, the top, bottom, and sides get a 1/4" groove at the table saw with the 1/4"-Kerf Flat-Top Blade for the back to slide into. This box is also assembled with pocket screws.
Follow along in the process with Part 2.
1 comment