Jointer & Planer Knives
Infinity Tools offers a wide selection of high speed steel and carbide knives for most planers, including DeWalt portable planers. Our high speed steel knives are designed to provide extended life and are forged from a premium grade of European D2 High Speed Tool Steel with a Rockwell hardness of 60 HRC to maximize abrasion resistence. our carbide tipped knives will last approximately 10 times longer than our premium HSS knives and feature high-grade micrograin carbide that has been permanently bonded to a rugged steel body.

Behind the table saw, arguably the two most used machines in the woodworking shop are the jointer and planer. These machines require precise setup and sharp knives to perform their best. Over the years I've picked up a few helpful tricks when it comes to getting the most out of these machines that I think a lot of fellow woodworkers may find helpful.
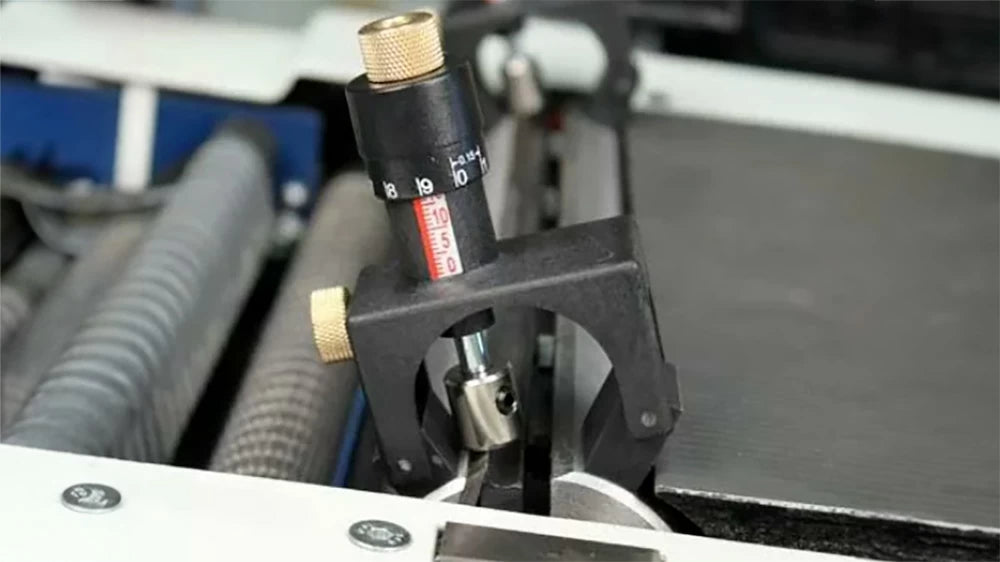
Here at Infinity, we carry both High-Speed Steel (HSS) and Carbide Tipped knives for a wide variety of machines. One question that comes up a lot is, should I do anything to the knives before I install them in my jointer or planer?
For the most part the answer is no, the knives are good to go right out of the box and perform beautifully. If, however, you want to bring the edge to the next level, a few quick swipes of the flat of the blade with a DMT Credit Card Sharpener will remove any burr that is left from the factory sharpening process and bring the blade to a keen edge. I typically think of this as a "feel good" step. Eventually, the super-sharp edge will dull a slight bit after a few cuts to a "working" edge where the knife will remain for most of its working life.

So, what's the difference between carbide and high-speed steel? Generally speaking, carbide will hold an edge as much as ten times longer than steel. Right out of the box, however, steel will feel sharper than carbide. Without getting into too much detail, this is due to the difference in grain structure between the two metals. While carbide will not take as sharp of an edge as steel, it will hold that edge much longer. A good quality Infinity HSS set will hold an edge 3 to 4 times longer than a stock replacement steel blade available for many machines.

Another factor that may influence your decision to go with HSS or carbide is sharpening and downtime. There's no doubt about it that carbide is a little more difficult to sharpen. But with the right tools, it's an easier task.
The advantage of carbide is that the cutting edge is considerably longer-lasting, requiring less sharpening which reduces machine downtime. If you tend to avoid replacing or maintaining the knives in your machinery, then carbide is a great choice. If you want to save money and don't mind the maintenance process, HSS is a good choice because you can squeeze a little more performance out of it with regular maintenance.
If you are inclined to do your own sharpening, there are a few tools that can make the job easy. The first is a Diamond Knife Hone. This can be used with the knives still mounted in the machine's cutter head. Diamond knife hones are great for keeping your knives in top shape when used regularly. They do require that the knife be adjustable in the head and that there's enough clearance for the hone to fit inside the machine to get to the knives. This can be tricky on some planers, but usually pretty easy on joiners.


The second option for sharpening joiner and planer knives is the Deulen jointer and planer knife sharpening jigs. These jigs hold a pair of knives at the correct angle so that they can be sharpened on a piece of wet/dry sandpaper or with a diamond sharpening stone. If you have large nicks in your knives you may need to send them off to be reground, but for normal sharpening, this is my favorite method.

Planers like the Dewalt 734 and 735 have become extremely popular. These planers use indexed knives. Indexed knives are those with holes or notches that are used to locate the knife in the cutter head.
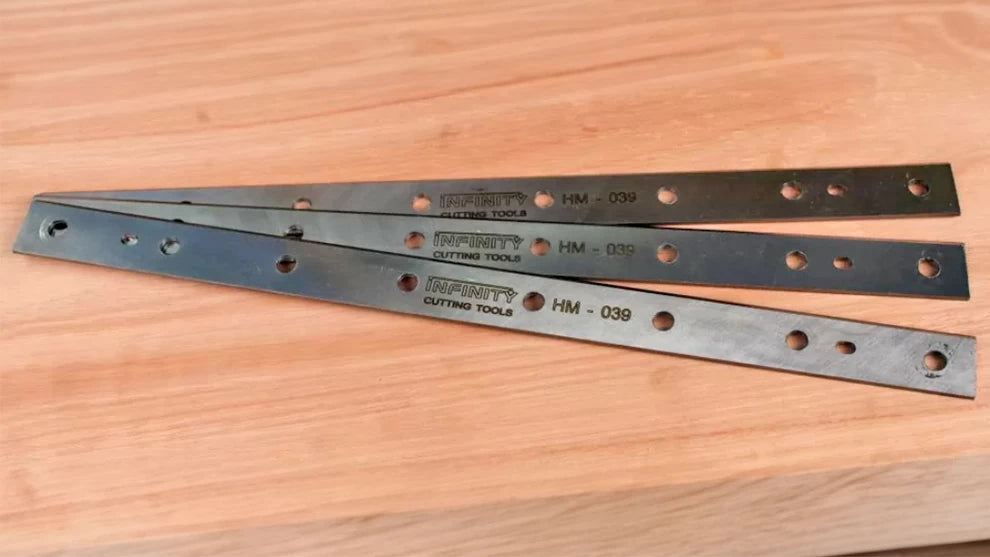
The big advantage of this style of knife is that they're very easy to set and replace because no special setup tools are needed. They're often dual-sided having two cutting edges per knife, basically turning each knife into two. The disadvantage of an indexed knife is that little if any, resharpening can be done to these knives. If too much material is removed during sharpening the knife becomes too short and can cause the cutter head to hit the workpiece instead of the knife.
The amount of material that can safely be removed from indexed knives depends on the model but can be as little as .008". Another drawback is that the knives are typically proprietary to the specific model of planer, making it difficult to find high-quality replacement knives.
For indexed knives we recommend only a light honing to renew the edge. It's basically the same deburring process I mentioned earlier but with the addition of a careful pass or to down the bevel of the knife. Think of this much like using a sharpening steel on a kitchen knife. It can renew an edge that is in good shape, but it won't save an edge that is too far gone, nor will it remove nicks.
Installing standard straight knives in a joiner or planer can be a daunting task if you have never done the job before. Many machines come from the factory with a tool that's used to set the knife to the proper height in the cutterhead. But if you're like me, the chance of finding these elusive tools is rare.
The first thing to do in either case is track down a copy of the owners manual and look for the setup instructions. In my experience these manuals can be found online for free download from a number of sources with a little digging.
If a machine is operating properly with knives that just need sharpening or replacement and no factory setup tool is available, a pair of planer knife-setting jigs may be the perfect solution. Because they can be set to the height of the knives in the machine, you can duplicate the original setup pretty easily.

For jointers, a jointer knife jig may be the perfect option because it allows you to set the knife to be perfectly in line with the out feed table of the joiner. This insures a snipe free cut and is especially helpful on jointers that don't have an adjustable outfeed table.